Logistics managers perform one of the most important roles within any business. They oversee the purchase and delivery process across the complete supply chain, from the initial delivery of raw materials for production to the final shipment to customers.
Without this vital set of skills, the products we rely on for everyday life would never make it to their final destinations, and businesses would quickly be overtaken by competitors. It means that, while logistics management is a high stakes role, it is endlessly rewarding and a key position within any business.
Interested in a career in logistics? Let’s take a closer look at the roles and responsibilities of a logistics manager.
Supply Chain Management
Think of the supply chain like a literal chain. Suppliers move products along each link, from raw materials through to production, warehousing and transport stages and on to the final sale. Logistics managers are responsible for holding each link of the chain in place, and this means working closely with stakeholders to ensure that the process stays on-track.
So what are the roles and responsibilities of a logistics manager in the supply chain? Traditionally, there are five distinct elements:
- Planning: Logistics managers need to plan for customer demand, using available data to ensure that the entire supply chain is able to meet expectations.
- Sourcing: Supply chains begin with suppliers, and logistics managers need to form and maintain supplier relationships. Tasks here also include paying suppliers, ordering, receiving and managing incoming inventory.
- Manufacturing: In many cases, products need to be manufactured with sourced raw materials. A logistics manager needs to ensure quality production, as well as shipping the manufactured product.
- Logistics: The role of logistics in supply chain management includes ensuring orders are shipped, coordinated and tightly scheduled for dispatch.
- Returning: Sometimes, the supply chain needs to double back to facilitate product returns for damaged or excess stock.
Transportation and Freight Management
The physical transportation of goods is a key role of logistics managers. There are many aspects to ensuring effective transport and freight, including:
- Carriers: Some organisations will transport their own goods, owning the means of freight (such as trucks or ships). Where this is not possible, logistics managers will need to form and maintain relationships with third party carriers.
- Routes: Effective freight can mean optimising transport routes to save time or reduce risk, if you’re using an in-house fleet.
- Regulations and compliance: Transport – particularly across state and international lines – often requires a logistics manager to coordinate correct documentation and compliance with laws and regulations.
- Tracking shipments: Whether freight is provided in-house or by a third party, logistics managers need to stay abreast of where shipments are and when they’re due to arrive.
- Data and analytics: Logistics managers need to maintain oversight on freight data in order to hit targets, as well as to improve results in the future.
Warehouse and Inventory Management
A successful logistics manager will have a tight grasp on warehouse management and inventory control. Warehouse and inventory management are not the same, though there is some overlap. Each role can be broken down as follows:
Warehouse management: This role involves coordinating the people and processes that allow a warehouse to run effectively. This includes incoming and outgoing stock, stock location management, staffing, equipment and other administrative tasks such as rostering, repairs, cleanliness and scheduling.
Inventory management: This task is dedicated entirely to understanding and controlling the inventory (ie. stock) within a warehouse. This is typically performed with the aid of dedicated enterprise resource planning (ERP) software, which can automate and streamline many of the requirements. Inventory management will include stocktake, stock rotation, and tracking sell-by dates.
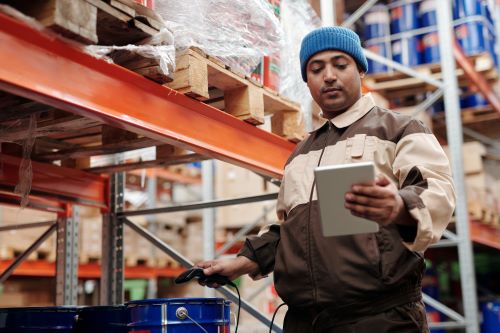
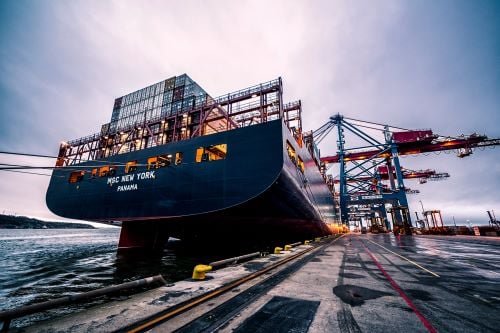
Risk Management
If there’s one recent shared experience for all logistics managers, it is the presence of risk. Although recent years have seen unprecedented disruptions to the supply chain, risk exists in logistics at all times and across the entire process. Successful logistics managers are the ones that plan for risk, create risk-mitigation processes within the business and who look at logistics holistically to identify potential risks.
Here are some areas of risks within logistics:
- Staff: Including industrial action and staff attrition (within the business and in suppliers/third-parties) as well as staff safety.
- Supply chain: Such as issues with suppliers and potential import/export restrictions.
- Manufacturing: Delays or breakdowns associated with machinery or production methods.
- Finance: Risks here include bankruptcy and cash flow issues.
Cost Optimisation
Inventory management is complex, with many moving parts. Though this can make holistic management a tough undertaking, it leaves plenty of potential for cost optimisation. This might include:
- Technological investment: ERP software in the warehouse, for example, can offer a reduction in human error, greater process automation and a greater deal of inventory oversight to prevent stock loss.
- Freight/transportation: Clever inventory managers may be able to optimise expenditure through transport route analysis, freight consolidation or off-peak shipping, as a few examples.
- Safety: Reducing lost time injuries (with proper safety training, for example) is just one way to ensure costs are saved by keeping workers healthy.
- Negotiation: Whether through bargaining, goodwill or mutual benefit, a shrewd logistics manager may be able to create cost savings by negotiating a better deal in areas like freight, materials supply or increased contract size/length.
Technology and Data Analysis
Technology has become indispensable to modern logistics operations, touching every aspect from material ordering to freight tracking and return automation. There are many examples of logistics ERP software that can assist logistics managers in uncovering issues like stock loss, faster transport options and even worker performance.
For example, inventory control software can make stocktake processes much faster than if they’re performed manually. This leads to time savings, a more accurate understanding of stock levels (by reducing human error) and a digitised data set that is easy to interpret.
Study Logistics Management
The world of logistics management is thoroughly rewarding. The role is constantly shifting, and no two days are ever the same for a logistics manager. Whether you’re passionate about global transport logistics or keen to delve into warehouse management, you’ll find everything you need with Monarch Institute transport and logistics courses.
Keen to find out more? Get in touch with our friendly team today.